Sustainability by Benninghoven
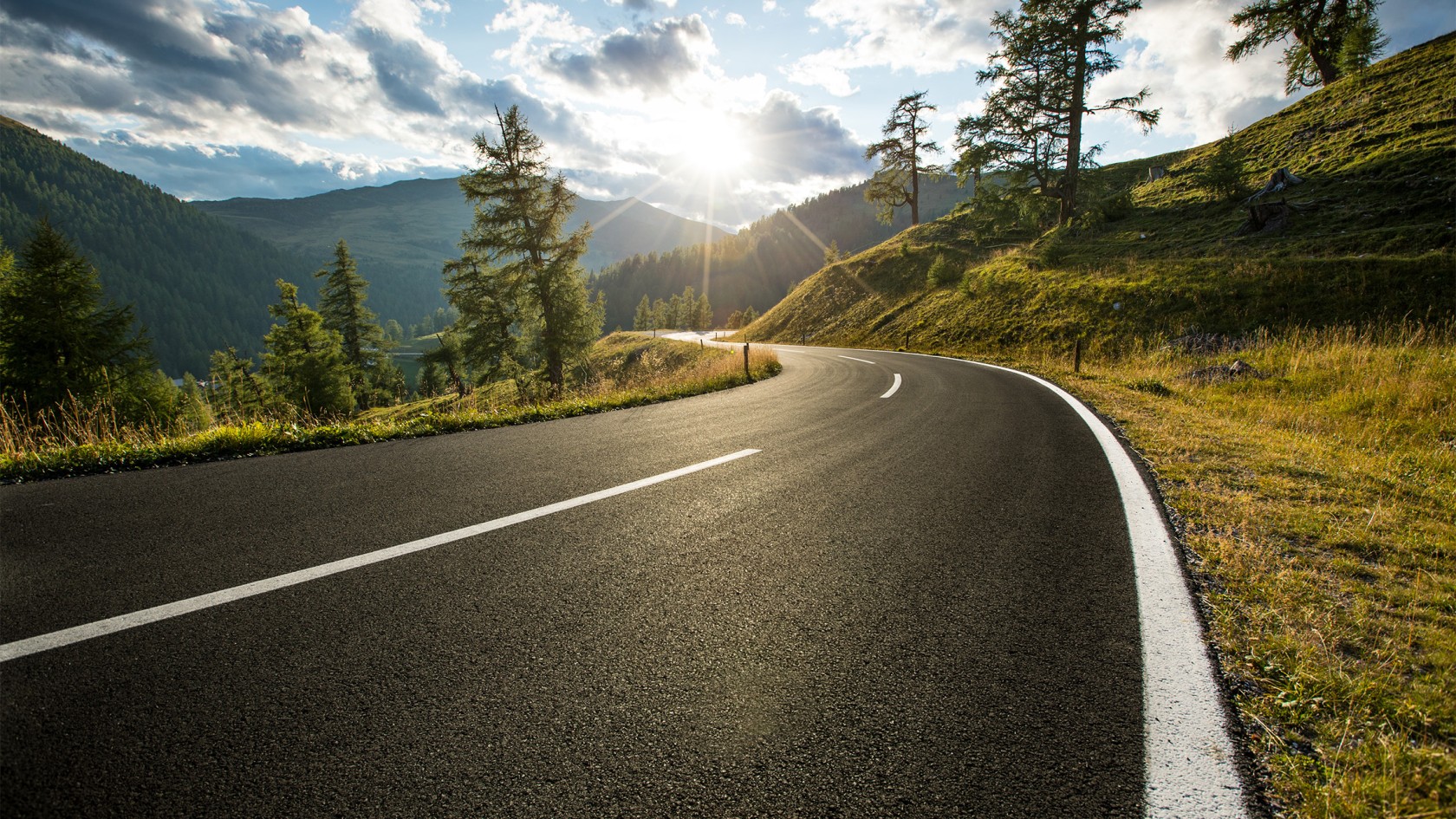
Sustainable solutions from Benninghoven lower emissions and secure the future of asphalt mixing plant sites.
Working more efficiently with sustainable and economical technologies is the challenge of today and tomorrow. Benninghoven offers a variety of innovative solutions for increasing sustainability in asphalt production. Considering at the entire road construction process, from the extraction of the materials to the production of the asphalt, right through to the construction of the road, plant operators can save up to 60 % of CO₂ emissions (annual production of 100,000 t of asphalt, 60 % recycled materials added, carbon-neutral fuel).
Benninghoven has decades of experience in recycling reclaimed asphalt. But reusing the material is not only sustainable. The material removed by milling the asphalt during road resurfacing is also significantly cheaper than virgin mineral from a quarry. In addition to this, reclaimed asphalt already contains bitumen, which is also reused and therefore saves on the most expensive ingredient in asphalt production.
Benninghoven offers different cold and hot recycling feed systems for this, including the leading recycling technology – the Benninghoven hot-gas generator. It allows up to 100 % recycling material to be added while maintaining low emissions. The Benninghoven REVOC system is a patented innovation that will be presented by Benninghoven at the Bauma 2022 exhibition for the first time. The new Retrofit solution is a supplement for existing asphalt mixing plants equipped with one or more recycling systems and it significantly reduces the total carbon concentrations in the exhaust gas. This also makes REVOC an important contribution to securing the future the plant site.
Learn moreFor an energy-efficient mixing process, resulting in low emissions such as CO₂, it is crucial to ensure the driest possible storage of virgin mineral and recycling materials. In this context:1 % more moisture in the starting material corresponds to a litre of additional heating oil or its energy equivalent for each ton of asphaltic mixture. This is one reason why covered storage is now required in Germany by the Technical Instructions on Air Quality Control (TA-Luft).
The drying and heating processes for virgin mineral and recycling material are particularly energy-intensive in asphalt production. Fuel and emissions can be saved if authorities and owners use reduced-temperature asphalt types. This refers to asphaltic mixtures with a final temperature of around 120 °C. This equates to a 30 % reduction in contrast to conventional mixtures, which usually require a temperature of around 160 °C. However, the potential savings in terms of energy and CO₂ are far greater:18,000 kWh and 6,000 kg of CO₂ are saved in the production of 2,000 t of asphalt – on a daily basis.
Benninghoven Asphalt mixing plants can produce high-quality reduced-temperature asphalt in a reliable process. One important technology for this is a foam bitumen module, which Benninghoven also offers as a Retrofit solution (plug & work). Foam bitumen is interesting because this binder requires only one auxiliary material for producing reduced-temperature asphalt: water, which is already available at any asphalt mixing plant anyway. Mixing hot bitumen with water multiplies the volume many times, which is why this process is also referred to as “foaming” the bitumen. The released surface energy ensures that the binder moistens the mineral very well during the mixing process even at low temperatures, temporarily generating installation properties that are comparable to those of hot asphalt.
Learn moreFor storing the hot bitumen – one of the most important asphalt ingredients – Benninghoven offers bitumen tanks with different capacities. These come with one or multiple chambers and can additionally be equipped with an agitator or a mixing nozzle.
With electrification, plant operation produces zero local emissions – in contrast to tanks with thermal oil heating. In terms of the carbon footprint, this ensures carbon-neutral storage of bitumen. In addition to this, electrically heated tanks are not regulated by environmental authorities and there are consequently no environmental restrictions.
Learn moreMore sustainability in asphalt production means moving away from fossil fuels such as coal and oil. Benninghoven already offers EVO JET burners that use the fuels of the future. These fuels consist of renewable raw materials and have a carbon-neutral footprint. They include biomass to liquid (BtL) fuels and wood dust. Even the complex process of burning wood dust results in a smooth flame pattern – the prerequisite for reliable operation of the plant. The innovative solutions fromBenninghoven set new standards for burner technology.
Benninghoven technology can also be used for modern fossil, gaseous fuels such as liquid gas or natural gas. Switching from pulverised lignite to natural or liquid gas already cuts CO₂ emissions in half.
In addition to this, the Benninghoven development engineers continue to work on the sustainable and economical use of other fuel types. Using hydrogen, for example, could be an option for overcoming the challenges of the future.
Learn moreSustainability is a core value for BENNINGHOVEN and follows the basic principles defined by WIRTEN GROUP. So which specific activities and actions are pursued in order to achieve these goals?
Learn moreWelcome to the world of BENNINGHOVEN – our start page provides more information on our products, technologies, company, current projects and news...
Learn more